Forensic Engineering
This page describes the forensic engineering services I provide based on 38 years engineering experience. The page also gives examples of current and recent forensic and insurance cases that I have worked on. The Forensic page contains a lot of useful information, particularly in the examples of the different cases.
The information will help you decide if I can determine the cause of your client’s engineering problem or accident and estimate the cost of damages and repair.
What is Forensic Engineering?
Forensic engineering deals with the civil engineering aspects of legal problems.
Forensic engineers investigate and determine the physical and technical causes – the why and how, a building or engineering structure has failed or does not perform properly. As well, why an accident occurred causing property damage, injury or death.
Field and laboratory tests are carried out and observations made much the same as for engineering investigations in general. Data and evidence are gathered from this work, analysed, conclusions drawn and an opinion developed as to cause (see Guidelines page).
Forensic investigations are different in that they are carried out with particular care and thoroughness because litigation overshadows the forensic work.
Fortunately, most cases, as many as 97%, are resolved without going to trial, often on the basis of a thorough engineering investigation and a well written engineering report and opinion (see Writing Forensic Reports and Opinions, Guidelines page).
Consulting Forensic Engineering Services
My engineering services are separated into the following three categories:
- A preliminary assessment of the technical strength of a claim.
- If the claim has merit, collecting detailed information on the cause of the problem.
- Providing additional assistance to counsel if the claim cannot be settled and the matter proceeds to discovery and trial.
A. Preliminary Forensic Engineering Services
- Evaluate the technical strengths, weaknesses and merits of a proposed claim for damages - based on existing data and information, arising from problems with buildings and civil engineering structures and traffic and industrial accidents causing property damage, injury or death.
- Independent, peer review of forensic investigations, claims, reports and opinions by others (see Guidelines page for a detailed outline of what I cover in an independent review of reports by others).
- Outline scope of a thorough forensic engineering investigation of the problem (see Guidelines page for an outline of the steps I follow in designing a forensic investigation).
B. Detailed Forensic Engineering Services
- Forensic engineering and insurance investigation of the cause of an engineering failure, property damage or poor performance of an existing building or civil engineering structure.
- Forensic investigation of the cause of slip and fall, traffic, commercial or industrial accidents causing property damage, injury or death.
- Identify and analyse evidence and develop an opinion on the cause of an engineering failure or accident (see Guidelines page for information on how I analyse evidence and; “How to Develop an Engineering Opinion and Write a Forensic Engineering Report”).
- Draft report on the investigation and opinion of cause (see Guidelines).
- Evaluate, design and direct remedial work, and estimate the cost of damages.
- Thorough briefing of counsel on the cause of the engineering failure or accident and the significance of the findings of the forensic investigation.
C. Additional Forensic Engineering Services
- Assist counsel finalize evaluation of the strengths and weaknesses of a claim for damages based on the findings of a detailed forensic engineering investigation.
- Develop lines of questioning for testimony and cross-examination at discovery and trial.
- Attend discovery and trial, assist counsel identify evidence, discrepancies, contradictions and errors in testimony of opposing witnesses and experts; develop additional lines of questioning.
- Testify as an expert witness at discovery and trial.
- Review and audit civil engineering investigations and environmental impact assessments by others.
- Mediation and dispute resolution.
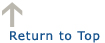
Examples of Current and Recent Forensic and Insurance Cases
Current and recent cases I have worked on are organized under the following categories:
These are cases that either involved civil litigation or litigation was being considered. Most were settled out of court - some after the engineering investigation was completed, others after discovery.
If possible, I indicate how the case was resolved and who was awarded damages, also who retained my services, counsel for the plaintiff or the defendant.
Each case is briefly described, the most important issue identified, the method of investigating the problem outlined and evidential findings given where possible.
I personally carried out the engineering investigations retaining other specialists to assist where necessary.
Most recently these specialists consisted of other civil engineers with a specialty different from my own. I have also retained a hydrologist, a metallurgist, a chemist, a structural engineer, land surveyors, and a metal detectorist (person who uses a metal detecting device to survey for the presence of metal fragments and objects buried in the ground at the scene of an accident or civil engineering failure).
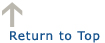
A. Retaining Wall Failures
1. UNB retaining wall failure
I carried out my first failure investigation while studying civil engineering during my 5th year at the University of New Brunswick. (This is an interesting case although not recent)
This was a significant and costly retaining wall failure but not a catastrophic failure like the bridge failure in Cape Breton, the landslide in New Brunswick and the gabion wall failure in Bedford.
The retaining wall failure undermined the foundations of the engineering building on the campus where we were taking lectures severely damaging the exterior walls of our 5th year classroom.
The engineering building was a two story brick structure. Damage to the building consisted of the exterior walls settling and shifting and quite large vertical cracks (I remember 1” to 2” wide cracks) opening in the corners of the building letting daylight into our classroom.
Consulting engineers for the university had hired a contractor to build a new engineering building adjacent our existing building. Construction involved digging a deep excavation adjacent the shallow foundations of the existing building.
The contractor installed a soldier pile shoring system to shore up the foundation soils supporting the existing building. This system involved driving steel piles into the ground to support horizontal timbers that would hold the foundation soils in place.
A soldier pile shoring system “gives” a little, deflects in engineering terms, in mobilizing its strength to hold back the foundation soils. The deflection occurs as the soldier piles bend a little along their length and tilt a little where they are driven into the ground. This is normal and a little movement like this is okay. Good engineering design keeps this movement to an acceptable magnitude.
In this case the soldier pile system deflected too much causing the foundation soils to yield or move sideways and settle in the process – causing the building walls to settle as well and the corners to crack and open up. The deflection was probably mainly due to tilting of the piles due to too shallow embedment and possibly some deflection along the length of the piles.
My investigation of this failure consisted of examining and taking measurements of the soldier pile system. I analysed the data, concluded the cause of the failure and submitted my student engineering report.
I passed my year so I must have got it right, not treading on any toes in the process – the engineers who approved the soldier pile system that failed were my professors who had formed a consulting engineering company to do this type of work. Failures occur in spite of the best efforts of the best people.
2. Gabion Seawall Failure
I was asked by the plaintiff, a property manager who was acting on behalf of a contractor, to examine a retaining wall that had collapsed during construction in Bedford.
The gabion wall was on the Bedford Basin. The wall was being constructed to reclaim land on the seaward side of a four unit townhouse property. The 10 foot high wall tilted over just before completion of the wall. It was rebuilt before I was retained.
At issue was the cause of the wall’s failure. This was in connection with a claim of damages against the designer and his insurance company. My investigation consisted of:
- Examining the site of the rebuilt wall.
- Studying photographs taken of the collapsed wall.
- Studying a design sketch of the wall.
- Interviewing two workers who were on the wall at the time it failed, including one who slid down with the wall on a piece of construction equipment as it failed.
- Interviewing the design engineer.
- Reviewing design principles for coastal and marine structures.
- Reviewing weather and sea conditions at the time of the failure.
I concluded, based on the evidence, that the wall failed because it was not designed properly. The principle defect was that the base of the 10 foot wall was not wide enough at three feet. I also found that the toe of the wall was not well protected against wave action in the Basin.
The professional engineer initially designed the wall properly specifying a six foot base. The engineer reduced the width to three feet during construction when the contractor said he was having difficulty building the wall as initially designed. The contractor also expressed concern about the stability of the townhouses and the slope up from the Basin if the original design was followed.
The matter was settled out of court and the design engineer’s insurance company covered the property manager and contractor’s losses.
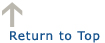
B. Fatal Accidents
1. Rankin Fatal MVA 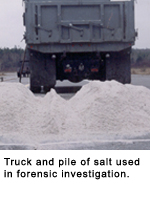
I was retained by the RCMP to investigate the cause of the motor vehicle accident that killed John Morris Rankin. Mr. Rankin died when he lost control of his Toyota 4-Runner and drove off a 75 foot cliff and into the sea.
The main issue was the effect, if any, of a pile of salt on the road on the cause of the accident.
My engineering investigation involved designing a field test and re-enacting the accident in field trials at the Shearwater airport.
I drove a Toyota 4-Runner over a pile of salt on a runway. The pile of salt on the runway was constructed to the same shape and size as the pile of salt at the scene of the accident.
The 4-Runner was driven initially at a speed of 20 km/hour (the fatal accident occurred at a speed of 50 km/hour or more) and the Toyota’s behaviour filmed from four vantage points on the ground and from a sea king helicopter flying overhead. The film was studied to determine the effect of the pile of salt on the cause of the accident.
The RCMP stopped the field trials when sufficient data had been obtained and it became too dangerous to continue at higher speeds without special safety precautions.
2. Jane Doe Fatal Aviation Accident
Ms. Doe was killed when her plane crashed on takeoff from Marsh Harbour Airport, Abaco Island, Bahamas.
I was retained by Dr. N. Clarke, a U.S. aviation accident reconstruction expert, to advise on the foundation soil conditions at the scene of the accident. The accident occurred near a runway where I had completed a foundation soil investigation prior to construction of the runway.
The main issue was whether or not the propeller on the port side of the aircraft could penetrate several 10s of centimeters into the ground at the crash scene, and this not occur on the starboard side.
My engineering investigation and advisory services involved a briefing by Dr. Clarke on the accident, studying photographs of the crash scene, reviewing my foundation soil report for the runway design and construction, and briefing Dr. Clarke on geological processes on Abaco Island and the probable soil conditions at the crash scene.
The case is still in litigation.
3. Swinimer Fatal Step Ladder Accident
The federal Department of Justice retained my practice to investigate the cause of a fatal step ladder accident. Mr. Swinimer died when he fell off a step ladder and hit his head while working above the ceiling of a cafeteria at CFB Greenwood.
The main issue was the effect, if any, of a bend in a leg of the step ladder on the cause of the accident.
I planned an engineering investigation that involved filming stuntmen re-enacting the accident by falling off a stepladder at the scene. This plan was preceded by examining the accident scene, reviewing military police documentation on the accident, submitting a preliminary report and offering an initial opinion on the effect of the bend in the leg of the ladder.
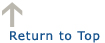
C. Slip, Trip and Fall Accidents
1. Adams Slip and Fall
A law firm retained me to investigate the cause of a slip and fall accident in Windsor, Nova Scotia. A sales representative slipped on a stair landing at the entrance to a store.
The main technical issue was the skid resistance of the material covering the landing.
My engineering investigation involved re-enacting the accident and filming what took place, determining weather conditions at the time of the accident, learning how the landing was cleaned, and the detergent used, and measuring skid resistance of a sample of the landing cover material.
My investigation found that the detergent used by cleaning staff in the store left a soapy residue on the landing that reduced the skid resistance of the floor covering.
The action was settled out of court.
2. Lederman Trip and Fall
I was retained by a law firm acting for the plaintiff to investigate the cause of a trip and fall accident in Truro. A pedestrian tripped and fell while walking along a sidewalk in the town.
The main technical issue was the condition of the sidewalk at the time of the accident.
My investigation involved a detailed survey of the accident scene and an examination of the materials and condition of the surface of the sidewalk.
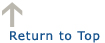
D. Airport runway failure
1. Andros Island International Airport, Bahamas
The Bahamian government, public works department, retained me to investigate the cause of holes that were appearing in an airport runway on Andros Island. The holes were several inches to a few feet in depth and breadth, and large enough to force closure of the international airport at the start of the tourist season.
The issues were the cause of the holes and how to repair them. There was also interest in the risk of future holes appearing in the runway.
My investigation involved:
- Examining the holes in the runway and the natural terrain beyond.
- Studying the published geology of the area, particularly the nature of the surface features characterizing the (the area was underlain by limestone exposed at the ground surface).
- Carrying out a ground penetrating radar (GPR) survey of the runway.
A GPR survey detects voids of any kind below the surface. The survey is often used to locate graves and buried bodies, features that were similar in size to the holes in the runway.
The investigation determined that the airport including the runway was located on Karst limestone terrain and that the holes were “banana holes”, a feature of this type of terrain.
Limestone dissolves in the presence of flowing water to form different kinds of cavities. The shape, size and location of the cavities depend on the conditions in the ground at the time. Banana holes are located near the surface of the limestone and sometimes have a thin roof of limestone - until the roof collapses.
There was a risk that more holes would form in the future. Data from the GPR survey identified zones below the runway that could be banana holes that would break through in time.
I recommended filling the existing holes with concrete reinforced at the surface with steel mesh. I also recommended proof-rolling the runway – passing a heavy vibratory roller over the runway to induce collapse of the roofs of banana holes before the wheel of a plane did this.
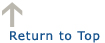
E. Building Problems
1. Vibrating Building
A home owner retained me to determine why his mobile home vibrated during the winter. The vibration occurred when he and his family walked from one room to another in their home. The owner also wanted to know why the interior partitions at some locations were separating from the ceiling.
The main issue was construction of the house foundations.
The engineering investigation determined how the building and foundation were constructed and how the building was supported on the ground. Field and laboratory tests determined the engineering properties of the foundation soils.
The evidence indicated that the home was supported on two continuous steel beams running the length of the mobile home. The beams were carried by concrete block piers at regular intervals supported on a sloping ground surface. The piers were founded above the depth of frost penetration. The ground was a dense, frost susceptible, silty glacial till.
Because of the sloping ground the height of the home above the ground gradually increased from 1.5 feet at one end to 3.5 feet at the other.
An analysis of the evidence concluded that frost was penetrating the ground to an increasing depth from the 1.5 foot end of the home to the 3.5 foot end. Heat loss from the home to the ground was less, and frost penetration greater, as the height of the home above the ground increased. As a result the piers were being heaved different amounts by the frost, and the steel beams lifted off the piers at some locations.
Sections of the mobile home were actually being “suspended” between piers at different locations. Walking from room to room caused the suspended part of the home to vibrate. It also caused the partitions to deflect and separate from the ceiling.
2. Building Settlement
I was retained by the owner of a dairy to determine why the foundations of a milk processing plant were settling, and then to correct the problem. The foundations were settling 10 mm per year 10 years after construction of the plant was complete – a lot of settlement in engineering terms so long after construction was complete.
The issues were the cause of the foundation settlement and how to stop it.
My investigation relied on a review of existing documentation on the earthworks development of the industrial lot, studying construction drawings of the plant’s foundations, drilling boreholes to confirm the findings of the document review, researching the engineering properties of filled ground, and reviewing ground improvement techniques.
Evidence from the investigation indicated that the foundations were settling because of the normal settlement of poorly compacted fill placed during development of the lot. Well compacted fills settle too but much less.
The settlement was stopped by injecting cement grout into holes drilled for the purpose – almost a mile of grout holes. The cement grout increased the strength of the fill and decreased its compressibility (settlement characteristics).
The owner’s claim for damages was settled satisfactorily out of court.
3. Undermining of Building
I was retained by the owner of a commercial building to assess the adequacy of the underpinning of the building’s foundations. I was asked to design remediation if this was necessary. The underpinning was carried out during construction of a building on an adjoining lot.
The issues were the adequacy of the underpinning and how to repair the underpinning if this was necessary.
The engineering investigation involved document review and a visual field examination – field testing was not necessary in this case although data from early stages of the repair reduced the cost of later work. The evidence found that the original underpinning was not adequate. Additional underpinning was designed and carried out.
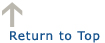
F. Environmental Problems
1. Toxic Air Quality
The owner of a new home retained me to investigate the cause of a toxic odour in the recreational room on the lower floor of his home. The odour did not occur on the upper floors of his home.
I was asked to review and evaluate the investigations carried out by two other consulting engineering firms and carry out any additional investigation that seemed necessary. One consulting firm worked for the house builder, the other for the home owner’s insurance firm.
The consulting firms had established that the odour was due to high concentrations of hydrocarbons in the air.
The consulting firm for the house builder concluded that the fumes containing hydrocarbons came from a solvent like paint thinner poured down a drain.
The consulting firm for the insurance company concluded, based on thorough testing, that the fumes came from a widely used sealant for vapour barriers.
The manufacturer of the sealant recommended using the sealant in a well ventilated area because of the fumes given off by the product and not to use it near heat.
Analysis by the consulting firm for the insurance company also demonstrated that the more preliminary work by the firm for the builder supported the conclusion that the sealant was the cause. Nevertheless, both the house builder and the insurance firm denied responsibility to the home owner.
The issues were:
- The adequacy of investigative work by the other two consulting engineering firms,
- Confirming or refuting the sealant as the cause of the toxic odour.
- Establishing why a widely used sealant was a problem in this house and not in others if that was in fact the case.
I resolved these issues by carrying out a thorough review of the work by the two consulting firms – a peer review, and doing nominal laboratory testing.
My evaluation of the work by the consulting engineering firms confirmed that the sealant was the cause of the odour. I also carried out additional field and laboratory work which established that the solvent had not been poured down a drain to cause the odour. This conclusion supported the same conclusion by the consulting firm for the insurance company.
I had additional laboratory testing carried out in the U.S. which established that the sealant used during construction of the house, the “job” sealant, was not defective. The U.S. testing also established the aged chemical properties of the job sealant.
My investigation established that the sealant caused a problem at this house because construction of the house resulted in formation of a poorly ventilated 1 ¾ inch void or cavity behind the walls in the recreation room. The void was located between the back of the 2 x 4 stud wall and the concrete foundation wall.
The cavity was poorly ventilated because it was located between the moisture barrier on the front of the stud wall and the inside surface of the relatively impervious concrete wall. Fumes were trapped in this cavity near the bottom of the void because the fumes were heavier than air.
The air in the cavity containing fumes with their high concentrations of hydrocarbons could not be “breathed out” to the open air, as house walls do, because of the impervious concrete wall. The fumes escaped to the recreation room through small holes cut in the bottom of the wall for the cable from the electric baseboard heater to cause the odour in the room.
The clue that this was the problem came to me when I recognized the similarity between the wall cavity and the space or “cavity” in a glass jar used in one of the laboratory tests. The test involved placing a sample of the job sealant in a closed jar with empty space – a cavity, and measuring the type and concentration of hydrocarbons in the air in the space/cavity in the bottle after a period of time.
The problem did not exist on the upper floors of the house where the sealant was also used. This was because the clapboard sided exterior walls were more porous than the concrete foundation walls and breathed the fumes to the outside.
My work also established that the odour problem had essentially passed by the time all engineering investigative work was completed. The sealant had given off more than 95% of its fumes by this time as established with the U.S. laboratory testing. This cessation of the problem may have been the case by the time I was retained by the owner but this could not be known at the time.
This was an interesting problem requiring a civil engineer to have knowledge of building construction and sufficient knowledge to read laboratory test results by chemists and to carry out additional laboratory testing to fill in the gaps.
The owner claimed damages in Small Claims Court against the contractor who built the house but lost because he presented his own case and did not do this so very well.
2. Residential Furnace Oil Spill
A home owner in Halifax retained me to assess the adequacy of the clean-up of his property which was contaminated by a fuel oil spill on his neighbour’s property.
The issues were the adequacy of the clean-up and the adequacy of future monitoring of the property.
I confirmed that the property was being cleaned up according to good engineering practice. To do this I inspected daily the methods being used on site – “dig and dump” of the contaminated soil, and the results being achieved. I also met daily with the consultants responsible for the clean-up.
However, while the property was cleaned up adequately, the proposed future monitoring was assessed as inadequate. Monitoring wells were proposed, which was a suitable method, but the wells were too few in number to confirm that the plume of contamination had passed. The owner took this discrepancy up with the consultant involved and in time through litigation obtained a portion of the damages he claimed and certification that his property was clean.
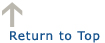
G. Tunnel failures
1. Vanier Tunnel, Bathurst
An insurance firm in Quebec retained me to investigate the cause of the misalignment of a small tunnel beneath a highway on the outskirts of Bathurst, New Brunswick.
The 18 inch diameter steel tunnel was designed to carry a gravity storm main on a slight grade beneath the highway. A machine designed for the purpose drove the 120 foot long tunnel by vibration at a depth of 25 feet beneath the highway. The tunnel was driven several inches off line during construction, sufficient to prevent gravity flow in the storm main.
At issue was the cause of the misalignment. The information would be considered in a claim by the municipality against the contractor.
My investigation included:
- Studying the results of the geotechnical investigation of the foundation soils carried out before the tunnel was designed.
- Reviewing design of the tunnel.
- Learning the construction method used to install the tunnel.
- Studying the soils geology of the area.
- Determining the type of soils beneath the tunnel site with additional boreholes and field testing.
- Interviewing a local well driller.
- Researching the engineering properties of the soils found beneath the site.
- Analysing the effect of vibrating the tunnel into place on behaviour of the soils.
The investigation found that the soils along the alignment of the tunnel liquefied and turned to a slurry when vibrated. The soils were a loose mixture of saturated sand and silt. The initial investigation of the soils missed this liquefiable characteristic of the soil.
Casual remarks by the local well driller on the nature of the soils in the area were quite invaluable.
I concluded that the vibration associated with the method of installing the tunnel caused the tunnel to misalign.
The claim against the contractor was not allowed for reasons other than the technical findings of my investigation.
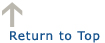
H. Bridge Failures
1. Rural Bridge Failure
I was retained by the plaintiff to investigate the cause of a bridge failure in Cape Breton that has permanently disabled a female car driver.
I carried out a detailed engineering investigation, identified the cause of the failure and issued an opinion.
The matter is in litigation at present and I am not at liberty to discuss it.
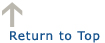
I. Landslides and Slope Failures
1. Filled Ground
I was retained to investigate the stability of a slope along a hiking trail constructed in Dartmouth, Nova Scotia.
The trail was near the bottom of a slope down to Halifax Harbour. The slope had been undercut in forming the trail.
The issues were the stability of the slope and the risk to the public. The results of the investigation would assist in assigning responsibility between the builder of the trail and the designer.
My investigation involved studying and comparing old and new topographic maps of the area, measuring the slope, examining the condition of the slope at and above the hiking trail, and studying the vegetation on the slope.
I concluded that the slope was formed in a deep, old fill, that it was unstable before the trail was constructed as evidenced by the curved trunks of small trees on the slope, and that cutting into the slope to form the trail as required by the design had increased the instability.
My assessment of increased instability followed from basic engineering principles for slopes. It was supported by field evidence in the form of new scarps on the slope above the hiking trail.
2. Urban Slope Failure
I was retained by the plaintiffs to investigate the cause of a slope failure that damaged the plaintiff’s property.
The main issue was whether or not undercutting the toe of the slope by the owner of a adjacent property caused the slope failure.
I carried out a detailed engineering investigation, identified the cause of the failure and issued an opinion. The matter is in litigation at present and I am not at liberty to discuss it.
3. Redhead Landslide
A landslide on the Fundy coast in New Brunswick destroyed a home. The owner asked that I examine the landslide in connection with a claim for damages. The owner’s home was located a few 10s of feet in back of the slope down to the sea.
At issue was the cause of the landslide and the risk of future failures in the area.
My investigation consisted of reviewing an existing research report by others on the engineering properties of the soil conditions underlying the area. I also examined the appearance of the landslide in the field making notes of surface features characterizing this particular landslide.
The investigation concluded that the landslide occurred due to natural processes.
The sea was continually scouring and eroding the toe of the slope gradually steeping the slope in the process. Research found that slope failures had occurred in this area in the past. The slope was formed on a deposit of red clay. The slope was held up by the strength of the clay, until a point was reached when the slope was too steep for the clay’s strength. The slope then slid down, in this case taking part of the owner’s house with it.
Landslides like this are sometimes “triggered” by another event. On this occasion rain fell in the area a few hours before slope failure. The rain water that collected in the ground had the effect of momentarily reducing the strength further. The water also increased the weight of the soil forming the slope; the heavier the soil the more difficult it is to hold up.
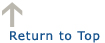
J. Drainage and Flooding Problems
1. Swimming Pool Failure
The owner of a swimming pool retained me to determine why the vinyl
liner of his pool was drifting or floating away from the sides of the pool. This occurred most years after installation of the in-ground swimming pool in 1989.
The liner supported by rigid steel panels contains the water in the pool. The panels are embedded in concrete footings and backfilled with a relatively free draining soil. The vinyl liner was designed to be held in place against the panels by the water pressure inside the pool.
The issue was the cause of the liner pulling away from the panels and whether or not this was related to construction of the pool.
My investigation involved determining how the pool was constructed by taking measurements in the field and excavating test pits just outside the pool.
Quite valuable information was obtained by interviewing two construction workers separately who reported essentially the same conditions behind the walls.
I also determined how the pool should have been constructed by talking with installers, reviewing manufacturer’s literature, reviewing engineering design principles, reviewing the guidelines published by national organizations, and examining pools under construction elsewhere in Nova Scotia.
The investigation concluded that the pool was constructed without an exterior drainage system in poorly drained natural soils.
It was possible for water to collect on rainy days in the porous, free draining backfill behind the panels. However, the rain water couldn’t drain away through the natural soils. As a result the water level rose behind the panels until it was higher than the water level inside the pool. The outside water seeped through construction joints in the panels to collect behind the vinyl siding and, because of the greater water pressure outside the pool, push the vinyl siding inwards causing it to float suspended in the pool water.
The problem was solved by constructing a simple drainage system that led the water away from behind the panels. The system consisted of drainage pipe embedded in porous gravel in a trench leading away from the pool; essentially, a French drain.
The owner claimed damages from the contractor who installed the pool.
2. Flooded Pump Room
The insurers of a community centre with an indoor swimming pool retained me to establish the reason the pump room in the basement had started flooding. The pumps in the basement were part of the operating system for the swimming pool.
The community centre was located adjacent a recently constructed multistory building with a two level basement parking area. The community centre was constructed several decades before the multistory building.
The issue was the cause of the flooding and whether or not this was related to construction of the multistory building and parking garage next door.
Investigation established that the community centre had a sump pump system in the basement but this had not operated properly for years. The basement flooded a little on occasional over the years but not to the depth of several feet that had occurred recently. As well, the basement floor was now continually wet with a thin film of water flowing across it. There was no significant change in rainfall in the area over the years.
The floor of the parking garage was dry. The garage also had a sump pump system in place.
I carried out an as-built survey that indicated the parking garage floor was about 21 feet below street level and well below the community centre pump room floor.
The concrete wall of the parking garage was within 10 feet of the community centre basement wall.
Discussions with a hydrogeologist established that the water table was usually just below the ground surface in this area. This would be the reason that both the community centre and the parking garage had sump pump systems in their basements. The water forming the water table flowed from the community center towards the parking garage.
Constructing the deep parking garage would be expected to lower the water table beneath all buildings in the surrounding area – the garage is a deep “hole” in the ground. Water tables drop to some extent near large holes in the ground.
But this was not happening in this area. The water table was in fact higher in the vicinity of the community centre as evidenced by the more severe flooding on occasion, and the continuous flow of a film of water across the pump room floor.
In reflecting on this I realized that the parking garage walls were relatively impervious compared to the ground through which the groundwater flowed – the ground was porous, closely jointed slate bedrock.
If the basement walls were also backfilled with a poorly draining soil, as often happens contrary to good design and construction practice, this would compound the problem. Free draining backfill to basement walls allows groundwater to flow down to a drainage system around a deep parking garage.and led away.
What was happening at the community centre was that the water table was welling up “up-stream” of the impervious concrete garage walls and poorly draining backfill much like water in a stream wells up on the up-stream side of a boulder in the streambed.
I concluded based on this analysis that the flooding in the community centre basement was caused by construction of the two level basement parking garage.
3. Cause of flooded land
A home owner retained me to investigate the cause of flooding in his area. He had been sued by his neighbour for causing the problem when he filled in a depressed area adjoining the neighbour.
The neighbour also alleged that an access road on a public right of way to the sea (Northumberland Strait) had been undermined by the flooding and could not be used by vehicles.
The issue was the cause of the flooding. A second issue was whether or not the road had been undermined and, if it had, was it caused by the flooding.
I investigated the cause of the flooding problem by arranging to have a detailed topographic plan made of the area. Study of the plan showed how the area was drained before and after the filling in of the depression.
I concluded that the filling in of the land by my client had caused flooding. Filling the area displaced more runoff and drainage water onto the adjoining land including flooding the access road.
I recommended removing the fill down to the original natural grade and my client agreed to do this. I inspected the construction work and was satisfied the area was restored to its natural state to the extent that this was possible
I investigated the reported undermining of the road by excavating test pits to learn about construction of the road and the subgrade soils.
I also carried out a field test that involved driving a loaded dump truck over the road and filming the reaction of the road to the weight on the wheels. Filming included close-up shots of the wheels in contact with the surface soils of the access road.
Based on the data from the test pits and the field test with the truck I concluded that the road had not been undermined.
The parties to the dispute accepted my findings and recommendations. Damages were awarded in the courts and the action brought to a close.
A property owner in Halifax retained me to investigate a similar problem to the above – the effect of construction and earthworks on her property on drainage across a neighbour’s property. The adjoining neighbour claimed damages associated with an increased flow of water across his property because of the earthworks.
Study of topographic mapping of the area, and a comparison of before and after (earthworks) runoff, found that the effect of the earthworks was negligible, and certainly would not account for the drainage of water across the adjacent property.
Before and after comparisons in connection with a situation are often key studies in forensic and insurance investigations.
The neighbour’s claim for damages was dismissed.
4. Flooded Residential Property
I was asked by a home owner to determine why the lower level of her home was flooding during heavy rain.
The issue was the cause of the flooding and whether or not this was related to drainage works carried out by the former owner of the property.
The home owner had recently purchased her home after the former owner acknowledged a flooding problem and reported fixing it.
The home was located near the bottom of a slope down from the road and near the side of very level ground to the rear of the property. The lower level of the home was finished including a finished floor over a concrete floor slab.
My investigation included:
- Drilling holes in the concrete slab and measuring the depth to the watertable below the slab.
- Excavating test pits to learn how the footing drain was constructed around the house.
- Uncovering and examining construction of the discharge pipe to the rear of the property as installed by the former owner.
- Measuring the grade of the discharge pipe.
- Measuring the difference in water level from the house to the rear of the property.
- Studying a video of the flooding and temporary pumping taken by the home owner.
The investigation found that the house was on the edge of a wetland. The repair reported by the former owner was not well done in that the discharge pipe was too small and not properly laid to grade. I also found that the grade to the rear of the property at the discharge end of the of pipe was very slight.
The basic problem was that the house was built too low and too close to the water level in the wetland.
A simple but costly solution to the problem would be to raise the house three or four feet.
Another much less costly solution was suggested when the trench that was excavated to examine the discharge pipe was left open for several months. It was observed that the lower level of the house did not flood during rain storms because the water drained away along the open trench.
This indicated that a large diameter discharge pipe properly laid to grade would carry the rain water away from the house by gravity. This would be facilitated by installing additional drain pipe under the footings to drain the water from beneath the concrete floor slab.
If the large diameter pipe did not work by itself then a sump pump could be installed and flood water pumped into the large pipe.
5. Fashoranti Wet Basement
The owner of another home constructed below the water table in a wetland area saw a lot of dampness on the interior of his basement walls. The walls were stained at the locations of cracks in the walls. Mold was forming on the bottom of the walls.
I was asked to determine the cause of the dampness and the associated problems.
The main issue was whether or not the basement was properly constructed by the house builder, the former owner of the house.
Examination of the basement established that it was being drained by a properly functioning sump pump system. The system consisted of two pumps in diagonally opposite corners of the basement discharging to a drain that led away to a watercourse at the rear of the property.
Examination of the ground adjacent the exterior basement wall found that the ground was either level or sloping slightly down towards the wall. A test pit adjacent the wall established that the wall was backfilled with a fine grained, poorly draining soil. The footing drain was in place and reasonably well constructed.
I concluded based on the evidence that the dampness was caused by surface water draining towards the basement walls after a rain and down along the exterior of the walls. Moisture held in the poorly draining backfill was contributing to the dampness of the walls.
The surface water and moisture were also getting into the interior of the walls through the cracks, a path of least resistance to the water compared to the backfill and its poor drainage properties.
The basement was properly constructed except for the poorly draining backfill that was level or sloping towards the basement walls.
6. McGregor Wet Basement
I was retained by the plaintiff, the owner of a commercial property in Halifax to investigate the cause of the ground timber floor rotting. The property was a two story end unit in a triplex.
The main issue was whether or not discharge from a neighbour’s roof downspout flow into the owner’s crawl space and caused the floor to rot.
The floor was rebuilt prior to my commission so the rotting condition of the floor and the underlying crawl space and foundations could not be easily examined.
My investigation involved:
- A thorough visual examination of the terrain in the area and the rebuilt interior and exterior of the property, particularly the condition of the foundations.
- Field measurements including an elevation survey.
- Test pits to determine the type of soils in the area and the depth to the bedrock.
- Review of existing documentation, most notably photographs and a video taken during rebuilding of the floor, the report of the expert for the defendant’s insurance company, a written statement by the owner on the location of water and wetness in the crawl space, and a written report by one of the workers on the location of water in the crawl space.
- Review of additional written statements by workers and building inspectors involved during the rebuilding.
- Interviewing the contractor who rebuilt the floor.
- Assessing the reliability of the examinations and written statements by the various people involved in the problem.
- Studying causes of wood rotting in Canadian and U.S. manuals on wood and construction with wood.
- Drafting before and after rebuilt floor and foundation construction drawings.
- Applying principles of scientific reasoning, most notably developing a model of the situation at the property, using the model to predict results of discharge from roof downspouts, and comparing the predicted results to actual field data (this reasoning proved quite valuable in increasing confidence in my opinion on the cause of the rotting).
I concluded based on the evidence that rainwater discharging from the roof downspout was the principle cause of the floor rotting.
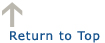
|